AN

certified company.
ET TMT is a part of Electrotherm India, a company founded in Gujarat, India, in 1983.
Electrotherm India is a well-diversified
holding company with a strong presence in
steel & pipe manufacturing, steel plant equipment,
transformers, TMT bars, battery-operated electric vehicles, renewable energy, transmission line towers and education.
Electrotherm India is a well-diversified holding company with a strong presence in steel & pipe manufacturing, steel plant equipment, transformers, TMT bars, battery-operated electric vehicles, renewable energy, transmission line towers and education.
A world leader in designing and manufacturing induction melting furnaces, we have a strong presence in continuous casting machines and ladle refining furnaces. We have supplied 6000+ equipments to steel plants across 71 countries in 40 years. All our products are Green Pro Ecolabel Certified.
A leader in Western India in steel manufacturing, Electrotherm provides solutions to steel plants from conceptualization to commissioning.
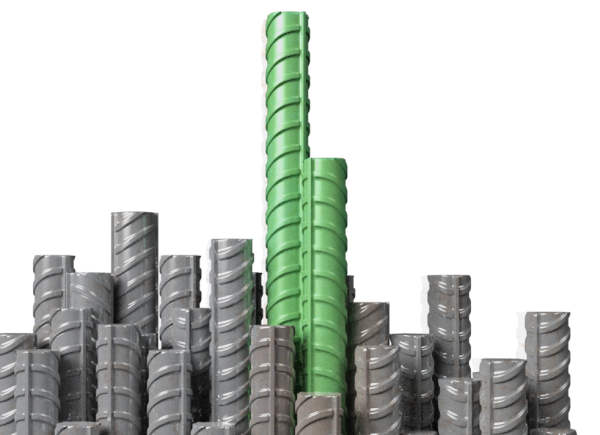
Raising the bar with
TMT BARS!
ET TMT is Western India’s first fully integrated facility
for manufacturing epoxy-coated, CRS, refined steel, superior quality steel, and cut and bend TMT bars.
In keeping with the ever-rising quality expectations of our customers, we at ET TMT endeavour to raise our standards through constant innovations to enhance process efficiency and product quality.
In keeping with the ever-rising quality expectations of our customers, we at ET TMT endeavour to raise our standards through constant innovations to enhance process efficiency and product quality.
EPOXY-COATING
Innovation at Work
Patented
Technology
ET TMT is Western India’s first fully integrated facility
for manufacturing epoxy-coated, CRS, refined steel, superior quality steel, and cut and bend TMT bars.
In keeping with the ever-rising quality expectations of our customers, we at ET TMT endeavour to raise our standards through constant innovations to enhance process efficiency and product quality.
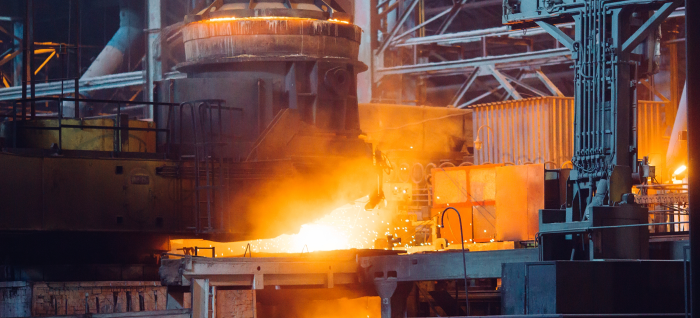
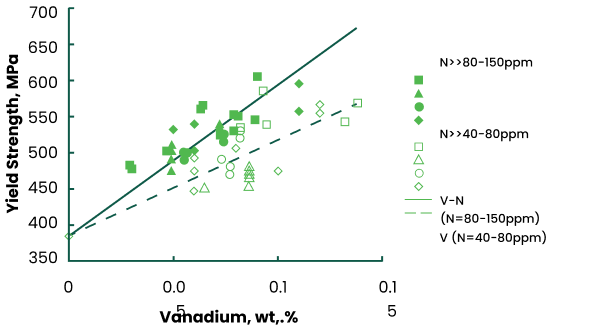
Innovative vanadium micro-alloyed steel
This steel has high ductility over a wide temperature range and is less prone to cracking during continuous casting & bending of rebar. Addition of 0.1% Vanadium results in savings of 10% to 15% on steel consumption and reduction of carbon footprint.
Relatively high ductility over a wide temperature range, vanadium steel is less prone to cracking during continuous casting at lower reheat temperature as well.
Vanadium is distributed uniformly during rolling resulting in low rolling loads.
Relatively high ductility over a wide temperature range, vanadium steel is less prone to cracking during continuous casting at lower reheat temperature as well.
Vanadium is distributed uniformly during rolling resulting in low rolling loads.
Ispat Agradoot Awards 2019 and 2022
Pioneering work in integrated Iron Ore-IF-LAF route to produce high-quality ET TMT Fe 500, Fe 500 D, Fe 550 & Fe 600 Bars won us the Ispat Agradoot Award in 2019.
Pioneering work in steel by using integrated BF + DRI → IF → LRF → CCM (EMS) → RM → ECP route to produce high-quality Fe 500 D TMT Bars won us the Ispat Agradoot Award in 2022. This route ensures less contamination in terms of tramp elements such as Copper, Zinc, Tin, Chromium, Nickel, Titanium etc., resulting in superior control over the chemical, mechanical & metallurgical properties of finished products in a wide range of steel grades as per varying applications.
Pioneering work in steel by using integrated BF + DRI → IF → LRF → CCM (EMS) → RM → ECP route to produce high-quality Fe 500 D TMT Bars won us the Ispat Agradoot Award in 2022. This route ensures less contamination in terms of tramp elements such as Copper, Zinc, Tin, Chromium, Nickel, Titanium etc., resulting in superior control over the chemical, mechanical & metallurgical properties of finished products in a wide range of steel grades as per varying applications.

Well-Equipped
Manufacturing Facility
Fully integrated sponge
iron kilns.
iron kilns.
Induction melting
furnaces.
furnaces.
Ladle refining
furnaces
furnaces
6/11 continuous
casting machines
casting machines
Continuous high-speed
rolling mill
rolling mill
Three-stage thermo-
mechanical treatment
mechanical treatment
Epoxy coating
plant
plant
Spectrometry
facility
facility
Cutting & bending
facility
facility
Blast furnace &
sinter plant
sinter plant
Ductile iron pipe plant
and utilities
and utilities
NABL-approved physical
and chemical testing
and chemical testing